Integrated fly ash/mortar slurry system (also known as integrated intelligent slurry station)
1. Pulping capacity: 30-120m ³/ H (conventional design requirement 25-50m) ³/ h) Meet audit requirements,
2. The integrated mobile fly ash/mortar/bentonite slurry system consists of the following main parts: slurry system, feeding system, secondary slurry storage tank, water tank, air compressor, offline monitoring system, accessories, and computer comprehensive control system,
3. Integrated sealed lifting design, convenient transportation and installation, and strong mobility. Adopting containerized sealing design.
4. The transmission part of the pulping machine adopts mechanical sealing, and the entire pulping process will not produce dripping or leakage, which is environmentally friendly and hygienic. The entire site is very clean.
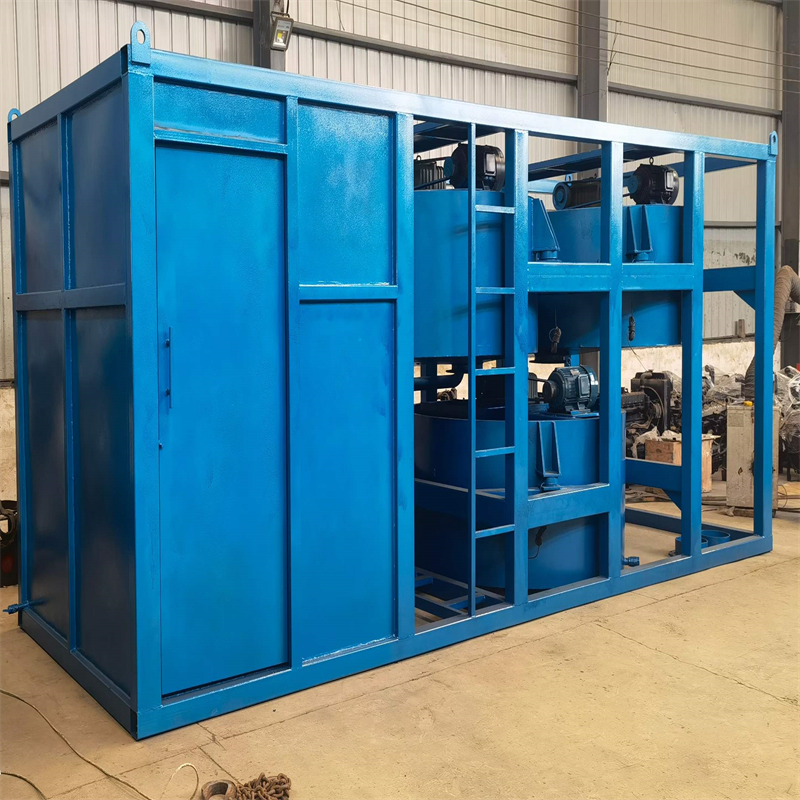
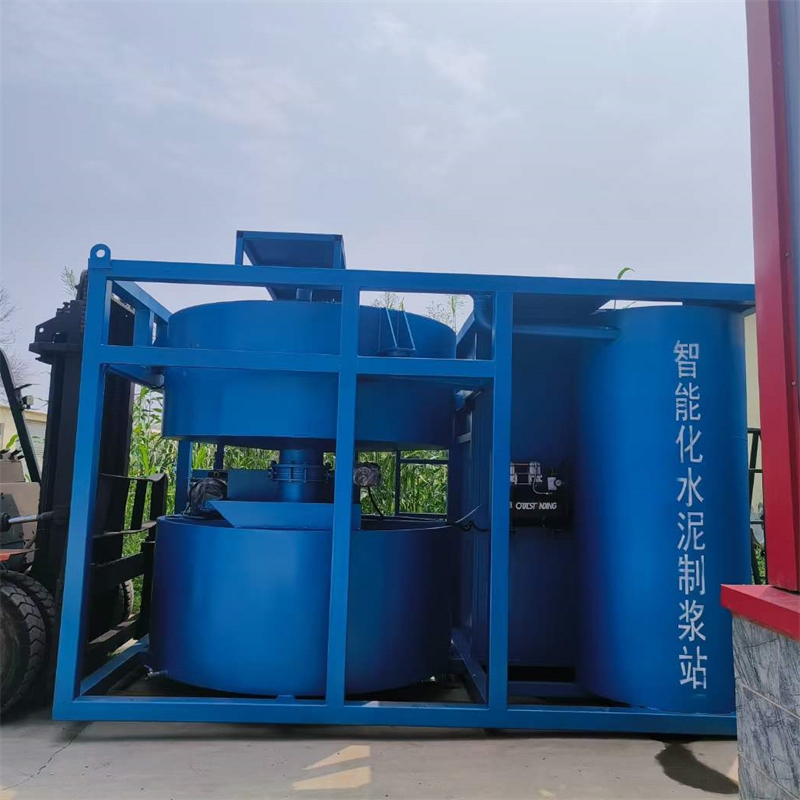
1、 Overview of mortar grouting system
The mortar grouting scheme has become the primary technical means of mortar grouting in China since the 1950s and has been used to this day. At present, the slurry production methods for ground grouting stations are manual or mechanical soil sampling and mechanical slurry production. Due to the inability to control the water volume, the concentration of the mortar cannot be controlled. The mortar grouting system produced by the company can continuously produce slurry, and can be adjusted for various flow rates, concentrations, etc. in conjunction with self-developed system software. This overcomes the shortcomings of previous grouting stations, such as large land area, high investment, high manual slag removal labor intensity, and low efficiency of filters.
2、 Model and specifications of mortar grouting system
The effectiveness and economy of grouting mainly depend on the selection of grouting materials, preparation of grout, transportation and grouting methods and processes. For different requirements (material, slurry concentration, conveying method, process), the company has designed the following series of grouting systems:
3、 The functions of the mortar grouting system
Function 1: Manual pulping. Require the system to deliver no less than 15m per hour ³- 20m ³ The slurry material (fly ash, ash) is fed into the slurry machine to produce a certain concentration of slurry. After thorough mixing, it enters the grouting site through a pipeline to achieve the grouting purpose.
Function 2: Automated pulping. By adding a certain proportion of slurry liquid for slurry production, it is then transported to the grouting pipeline network through a grouting pump to reach the grouting site.
Function three: Circular grouting. By adding a certain proportion of slurry liquid for slurry production, a composite grouting liquid can be formed and circulated to achieve an automatic circulation system. Then, it is transported to the grouting pipeline network through a grouting pump to reach the grouting site.
4、 Characteristics of mortar grouting system
Large pulp production volume and high pulp concentration can significantly reduce labor costs;
The system adopts mechanized quantitative feeding, which can adjust the conveying amount of pulp according to the required pulp volume or pulp concentration;
Through this system, the pulp raw materials can be fully integrated with water, the mud concentration can be controlled, and additives can be added to the slurry to form a colloidal mortar; Extending the time for the synergistic effect between water and slurry in the grouting treatment process;
The closed-loop control of the water supply system can automatically adjust the water supply and display the water supply in real-time.
The diameter of the pulp making machine and automatic feeding filter mesh can be equipped according to actual requirements, which can filter light floating objects such as grass roots, as well as heavy solid residues such as stones and bricks.
The use of immersion filtration slurry increases the mixing time between the slurry raw materials and water, not only improving the utilization rate of the slurry raw materials, but also making the slurry more uniform and achieving ideal gelation effect;
During the entire process of slurry preparation and transportation, the slurry flows out on its own using the weight of the equipment during the preparation, filtration, and grouting pipeline flow, greatly saving energy.
The slurry liquid is transported in a sealed pipeline, free from moisture, pollution, and climate conditions, while effectively protecting the working environment;
Using PLC programmable controller as the core component of the electrical control system, it can easily control various parameters, has a high degree of automation, and is suitable for the production needs of modern grouting;
The overall design of the grouting system is reasonable, with flexible operation, fewer operators, advanced technology, and safety and reliability.
Capable of achieving the pressure injection function of multiple grouting materials according to the prevention or emergency requirements of different operation methods;
Grouting materials can also use materials such as fly ash/cement, and our company can develop plans according to user needs.
5、 The process flow of mortar grouting system
The grouting system consists of a slurry storage site, a quantitative feeder, a screw conveyor, and other slurry quantitative, metering, and conveying systems, a continuous quantitative grouting system, a ground suspension agent addition system, a filtration and mixing system, a slurry pipeline network system, and an underground suspension agent addition system.
When grouting, the mortar is fed into the screw conveyor through a quantitative feeder, and the mortar is continuously and uniformly delivered to the slurry making machine according to the set fixed amount (adjustable conveying amount); A certain pressure of water is pumped into the slurry making machine through a water pump, and the slurry is mixed evenly. Then, logistics two enters the mixer for mixing, and the three are mixed evenly in a certain proportion. After entering the slurry storage machine for secondary mixing, the appropriate thickened suspension gel is produced. The main function of the slurry filtration section is to filter the slurry of different concentrations. Solid particles larger than 6mm in the slurry will be filtered out, preventing them from entering the grouting pipeline, to ensure that the grouting pipeline is not blocked due to the sedimentation of solid particles.
The grouting station also has a buffer tank, and the outlet of the filter is higher than the inlet of the buffer tank. The outlet of the filter is connected to the inlet of the buffer tank through the outlet pipe. When implementing underground grouting, the colloid in the buffer pool is introduced into the pump pool, and the slurry is pumped into the grouting pipeline from the ground to the underground through the slurry pump. It is then injected into the fire area through the mining mobile fire prevention and extinguishing grouting device to play a fire prevention and extinguishing role.
The grouting system consists of a slurry storage site, a quantitative feeder, a screw conveyor, and other slurry quantitative, metering, and conveying systems, a continuous quantitative grouting system, a ground suspension agent addition system, a filtration and mixing system, a slurry pipeline network system, and an underground suspension agent addition system.